Maximizing Efficiency with Electric Molding in Metal Fabrication
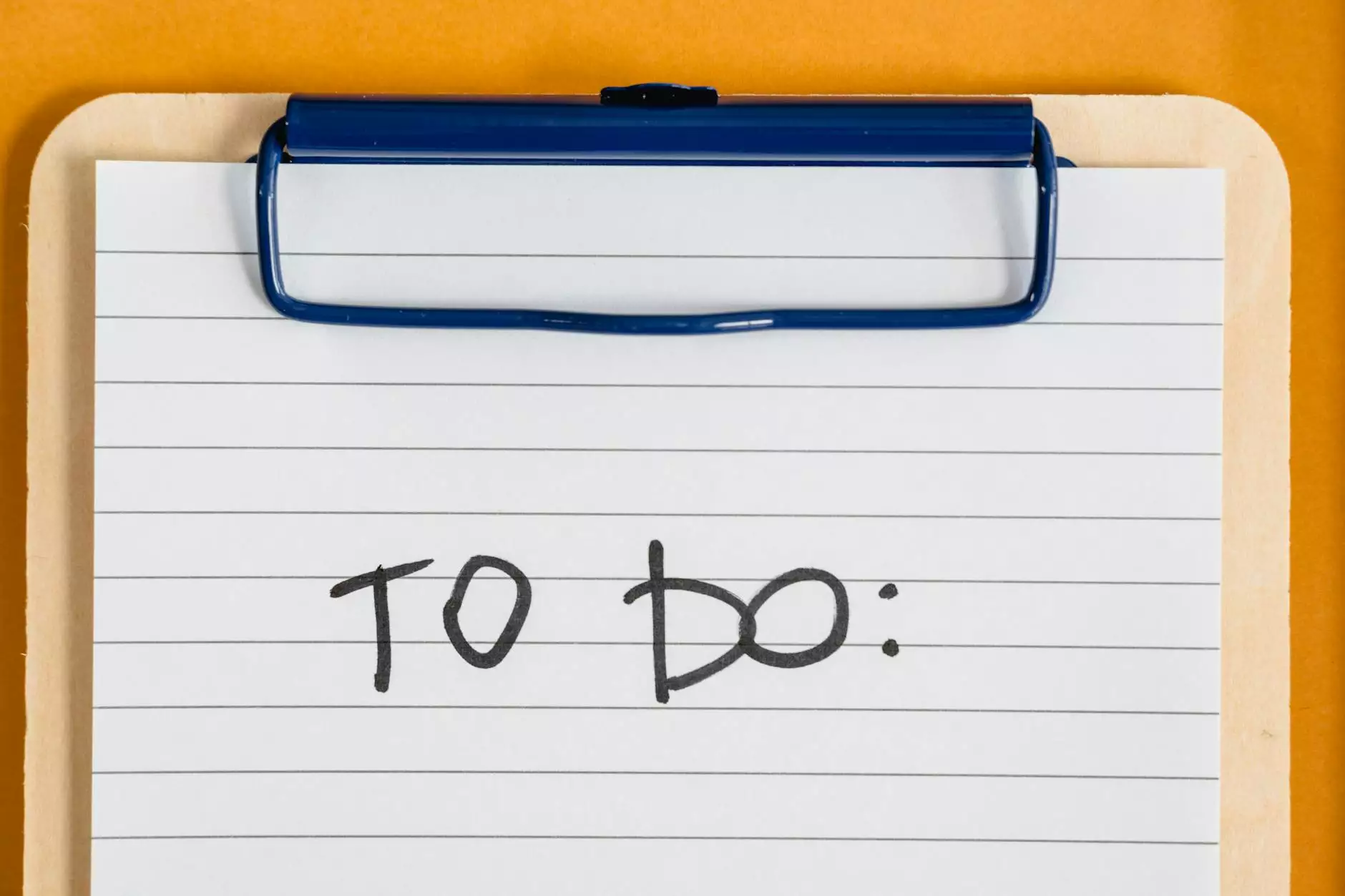
The realm of electric molding has emerged as a crucial innovator in the field of metal fabrication. It represents the forefront of modern manufacturing techniques, which are fundamentally altering how products are designed and produced. In this article, we will explore the various facets of electric molding, its advantages, and its application within the industry, particularly focusing on how businesses like Deep Mould are harnessing this technology to enhance efficiency and quality.
The Basics of Electric Molding
Before delving into the intricate details, let's start by understanding what electric molding entails. Essentially, it is a manufacturing process that utilizes electric energy to shape molten material—most commonly plastics or metals—into specific forms or products. This technique relies heavily on precision and advanced technology to achieve consistent and high-quality results.
How Electric Molding Works
The process of electric molding can be broken down into several key stages:
- Material Preparation: The first step involves selecting and preparing the raw materials that will be used in the molding process.
- Heating and Melting: The materials are then subjected to controlled heating using electric energy, causing them to melt into a pliable state.
- Molding: The molten material is injected into a mold where it takes on the desired shape, facilitated by advanced machinery.
- Cooling: The molded product is cooled to solidify it before removal from the mold.
- Finishing: Finally, any excess material is trimmed, and the product may undergo further processing to enhance its characteristics such as surface finish, strength, or durability.
Benefits of Electric Molding
The integration of electric molding into the metal fabrication industry brings forth a multitude of benefits. Here are some of the most significant advantages that have contributed to its growing popularity:
1. Enhanced Precision and Quality
One of the standout features of electric molding is its ability to deliver exceptional precision. Modern molding machines equipped with electric controls allow for fine-tuning of the process, ensuring that each product meets stringent quality standards. This level of accuracy minimizes defects and reduces waste, resulting in higher overall product quality.
2. Increased Production Speed
In today’s fast-paced market, speed is essential. Electric molding systems can operate at accelerated speeds compared to traditional methods. This not only boosts productivity but also allows manufacturers to meet tight deadlines and respond quickly to market demands.
3. Energy Efficiency
Compared to conventional molding techniques that require significant heating time and energy consumption, electric molding is known for its energy efficiency. The direct heating capabilities enable faster energy input and quicker cycles, ultimately leading to reduced operational costs and a lower carbon footprint.
4. Versatility in Applications
The versatility of electric molding is another compelling reason for its adoption. It can be employed across various industries, from automotive and aerospace to consumer goods and medical devices. This flexibility allows manufacturers to modify their production lines easily to cater to different products without substantial changes to equipment.
5. Reduced Labor Costs
Automating the electric molding process minimizes the need for manual labor. While skilled technicians may still oversee operations, much of the heavy lifting is done by machinery, which leads to reduced labor costs and the ability to allocate human resources to more strategic roles within the production process.
Applications of Electric Molding in Metal Fabrication
Electric molding is not solely limited to plastics. The metal fabrication industry has seen a significant uptick in the usage of this technique, with companies leveraging its capabilities for various products and components. Here are some key applications:
1. Automotive Components
In the automotive industry, precision and durability are paramount. Electric molding enables the production of complex parts such as brackets, housings, and gears with high accuracy. This contributes to enhanced vehicle performance and safety.
2. Aerospace Components
The aerospace sector requires components that meet rigorous specifications. Electric molding techniques allow for the creation of lightweight, high-strength parts essential for aircraft and spacecraft. This is vital for improving fuel efficiency and overall performance.
3. Consumer Electronics
With the rapid advancement of technology, consumer electronics demand components that are not only reliable but also aesthetically pleasing. Electric molding facilitates the production of intricate designs and finishes, offering manufacturers flexibility in product development.
4. Medical Devices
Healthcare products and instruments require the highest standards of quality. Electric molding meets these criteria by producing components that are sterile, precise, and compliant with strict regulatory requirements.
Advancements in Electric Molding Technology
The evolution of electric molding technology has brought forth several innovative advancements that have further cemented its status in the industry. These include:
1. Smart Molding Machines
Modern electric molding machines are now equipped with smart technology that enables real-time monitoring and adjustments during the molding process. This capability ensures optimal performance and allows manufacturers to quickly identify and rectify any issues that arise, leading to consistently high production quality.
2. Improved Mold Design
New advancements in mold design, including the use of computer-aided design (CAD) software, allow for more complex and efficient molds. This innovation not only enhances the end product's quality but also reduces the time taken to create and test new designs, ultimately shortening the product development cycle.
3. Integration with Industry 4.0
The rise of the Internet of Things (IoT) and Industry 4.0 has had a profound effect on electric molding. Smart factories can now integrate electric molding systems with other automated processes, creating a seamless workflow that enhances efficiency, data collection, and overall manufacturing intelligence.
Challenges and Considerations
While the advantages are substantial, it is important for businesses to consider the challenges associated with implementing electric molding systems:
1. Initial Investment
The upfront costs of acquiring sophisticated electric molding machines and technology can be high. Businesses must carefully assess their potential return on investment and operational needs when transitioning to this advanced manufacturing technique.
2. Technical Expertise
Implementing innovative molding technologies necessitates skilled personnel who can operate and maintain the machines effectively. Training and potential recruitment of skilled workers may add to overall costs and timelines.
3. Maintenance and Servicing
Electric molding machines require regular maintenance to ensure optimal performance. Establishing a reliable maintenance schedule is essential to prevent any disruptions in production and to prolong the lifespan of the equipment.
The Future of Electric Molding in Metal Fabrication
As technology continues to advance, the future of electric molding appears bright. Ongoing research and development are expected to yield even greater efficiencies, capabilities, and quality improvements in this sector. Considering current trends and the increasing need for sustainable manufacturing practices, companies are likely to continue adopting electric molding as a vital part of their operations.
Conclusion
In summary, electric molding stands at the forefront of metal fabrication innovation, providing unparalleled advantages in quality, efficiency, and versatility. For businesses like Deep Mould within the metal fabricators category, embracing this technology means not only staying competitive but also leading the way in modern manufacturing practices. By understanding its benefits and successfully navigating its challenges, manufacturers can pave the way for a more efficient, sustainable future in production.