Production CNC Machining: Revolutionizing Metal Fabrication
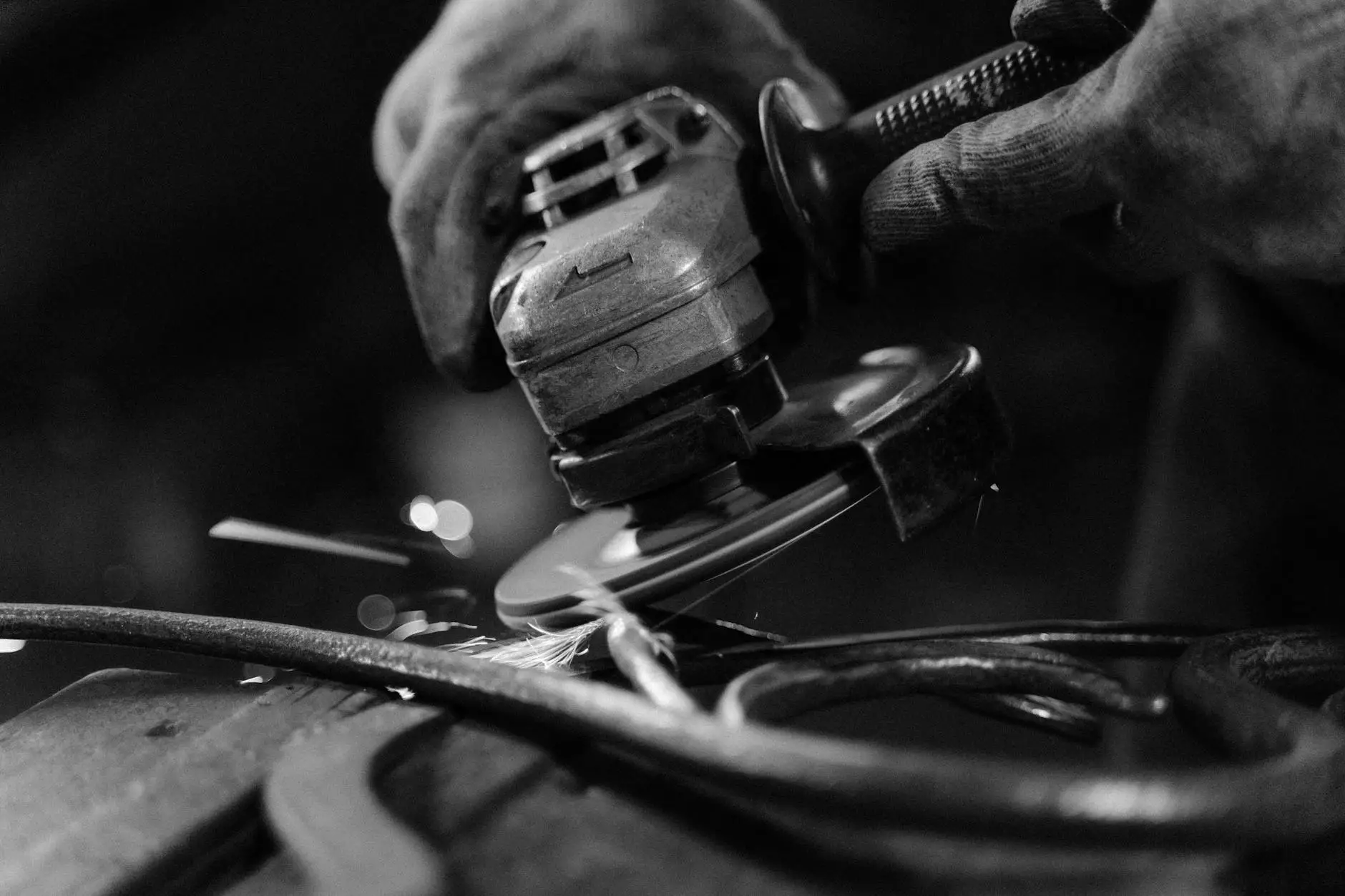
Production CNC machining has emerged as a cornerstone of modern manufacturing, offering unparalleled precision, efficiency, and scalability. As businesses strive to keep up with the demands of a fast-paced market, understanding the intricacies of CNC (Computer Numerical Control) machining becomes essential. This article will delve into the applications, advantages, and future of production CNC machining, particularly in the realm of metal fabrication.
What is Production CNC Machining?
Production CNC machining refers to the use of computerized equipment to control machine tools for manufacturing parts with high precision. The process involves using CAD (Computer-Aided Design) software to create designs, which are then fed into CNC machines. These machines interpret the design instructions and precisely cut, shape, and finish various materials, predominantly metals.
Types of CNC Machines Used in Production
There is a diverse array of CNC machines capable of fulfilling different production needs:
- CNC Milling Machines: Used for cutting and shaping solid materials. They can perform multiple operations including drilling, boring, and tapping.
- CNC Lathes: Designed for rotating workpieces while applying tools to the material, ideal for cylindrical objects.
- CNC Plasma Cutters: Utilized for cutting through metal plates using a plasma torch. These machines are fast and effective for thick materials.
- CNC Lasers: Apply high-powered lasers to cut or engrave materials with extreme precision.
- 3D Printers: Though not traditional CNC machines, they are used in the CNC family to manufacture components layer by layer.
The Importance of CNC Machining in Metal Fabrication
Metal fabrication is a vital industrial sector, where precision and quality play critical roles. Production CNC machining significantly enhances the metal fabrication process through:
1. Increased Precision
CNC machines provide a level of precision that manual machining cannot match. The computerized controls lead to minimal human error, ensuring that components are fabricated to exact specifications.
2. Enhanced Efficiency
The automation provided by CNC machining allows for faster production cycles. Components can be produced in large volumes without sacrificing quality, significantly improving operational efficiency.
3. Complex Designs Made Easy
With CNC machining, fabricators can create complex geometries that would be impossible or prohibitively expensive to achieve with manual methods. This opens up new avenues for innovation in design.
4. Material Variety
CNC machines are capable of working with a wide variety of materials including aluminum, steel, brass, and titanium. This versatility enables metal fabricators like Deepmould.net to tackle numerous projects across different sectors.
5. Scalability
As demand fluctuates, CNC machines can easily scale production up or down, making them ideal for both small-batch production runs and large-scale manufacturing.
Applications of Production CNC Machining
The versatility of production CNC machining lends itself to various industries:
- Aerospace Industry: Fabrication of complex parts that must meet stringent safety standards.
- Automotive Industry: Production of specialized components such as engine blocks, transmission cases, and more.
- Medical Device Manufacturing: Creation of precision parts required in medical instruments and implants.
- Electronics: Fabricating parts for consumer electronics, PCs, and servers.
- Construction and Heavy Machinery: Providing robust and reliable components for heavy-duty applications.
Benefits of Partnering with Experienced Metal Fabricators
Choosing the right partner for production CNC machining is critical for achieving project goals. Here are some benefits that experienced metal fabricators can offer:
1. Expert Consultation
Experienced fabricators bring a wealth of knowledge, enabling them to advise clients on design optimizations and material selection.
2. Quality Assurance
Companies like Deepmould.net adhere to strict quality control measures, ensuring that every part produced meets high standards of accuracy and consistency.
3. Advanced Technology
Utilizing the latest CNC technology not only enhances production capabilities but also ensures faster turnaround times and the ability to tackle complex projects.
4. Cost-Effectiveness
By streamlining processes and reducing waste, professional metal fabricators can offer competitive pricing without compromising quality.
Challenges in Production CNC Machining
While production CNC machining offers numerous advantages, there are also challenges to consider:
1. High Initial Investment
The cost of purchasing CNC machinery and software can be substantial, making it a significant investment for small businesses.
2. Skill Requirement
Operating CNC machines requires a specific skill set that may necessitate training and continuous education to keep up with technological advancements.
3. Maintenance Demands
CNC machines require regular maintenance to ensure they operate effectively, which can result in additional costs if not properly managed.
4. Software Dependence
The reliance on software for programming can be a double-edged sword; issues with software can halt production entirely.
Future Trends in Production CNC Machining
The landscape of production CNC machining is continually evolving, and several trends are shaping its future:
1. Integration with AI and Machine Learning
Artificial Intelligence is expected to revolutionize CNC machining by enabling predictive maintenance, optimizing machining parameters, and automating complex programming tasks.
2. Increased Automation and Robotics
The trend toward automation is growing stronger, with more companies adopting robotic arms and automated systems to enhance productivity and reduce labor costs.
3. Sustainability Practices
As environmental concerns rise, CNC machining operations are increasingly focusing on sustainable practices, such as waste reduction and energy efficiency.
4. Customization and Personalization
As market demands shift, there is a growing need for customized solutions. CNC machining provides the flexibility to design and manufacture tailored products efficiently.
Conclusion: The Role of Production CNC Machining in Modern Manufacturing
Production CNC machining is pivotal in driving forward the capabilities of metal fabrication. Its advantages in precision, efficiency, and the ability to handle complex designs have made it a preferred choice in multiple industries. As businesses like Deepmould.net continue to innovate and invest in advanced CNC technologies, the future of CNC machining looks promising, filled with opportunities for growth and expansion.
For those in the metal fabrication realm, embracing production CNC machining is not just an option; it is a necessity to stay competitive and meet the changing demands of the market.